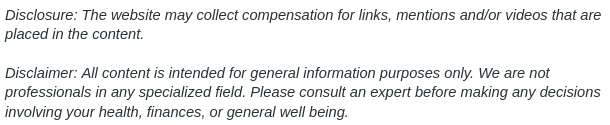
When it comes to welding, TIG (Tungsten Inert Gas) and MIG (Metal Inert Gas) are two popular methods. Each has its advantages and disadvantages, and choosing the right one depends on your project needs. This article will help you understand the pros, cons, and best uses for both TIG and MIG welding.
TIG Welding
Pros:
1. Precision and Control: TIG welding offers superior control, allowing for precise welds. This makes it ideal for projects requiring high detail and a clean finish.
2. Versatility: TIG welding can be used on a wide variety of metals, including steel, stainless steel, aluminum, and even exotic metals like titanium.
3. Aesthetics: The welds produced by TIG welding are often more aesthetically pleasing. This makes it a popular choice for projects where the appearance of the weld matters.
Cons:
1. Time-Consuming: TIG welding is a slower process compared to MIG welding. The precision and control come at the cost of speed.
2. Learning Curve: It takes more time to learn and master TIG welding. It requires steady hands and good coordination.
3. Cleanliness: The metal surfaces need to be meticulously cleaned before welding. Any contaminants can affect the quality of the weld.
Best Uses:
TIG welding is best for projects that require a high level of detail and clean, strong welds. It is commonly used in the aerospace industry, automotive work, and when creating custom metal parts. It is also ideal for food grade welding, where cleanliness and precision are crucial.
MIG Welding
Pros:
1. Speed: MIG welding is much faster than TIG welding. It’s efficient for long welds and larger projects.
2. Ease of Use: MIG welding is easier to learn and use. It’s more forgiving and less skill-intensive, making it suitable for beginners.
3. Material Preparation: MIG welding requires less meticulous cleaning of the metal surfaces. It can handle materials that are not perfectly clean.
Cons:
1. Less Precision: MIG welding does not offer the same level of control as TIG welding. The welds might not be as clean or detailed.
2. Gas Changes: Different materials often require different shielding gases in MIG welding. This can be inconvenient and adds to the setup time.
3. Aesthetics: While you can achieve good-looking welds with MIG, they generally won’t be as aesthetically pleasing as TIG welds.
Best Uses:
MIG welding is perfect for projects that require speed and efficiency. It’s widely used in construction, manufacturing, and for repairs. It’s also great for hobbyists working on home projects or building items like go-kart frames.
Conclusion
Both TIG and MIG welding have their place in the world of metal fabrication. TIG welding is the go-to for precision, clean welds, and versatility across a range of metals. It’s ideal for intricate projects and situations where the appearance of the weld is important, including food grade welding. MIG welding, on the other hand, is valued for its speed and ease of use, making it perfect for larger projects and beginners.
Choosing the right welding method depends on your project requirements. If you need detailed, aesthetically pleasing welds and are working with a variety of metals, TIG welding is your best bet. If you need to complete a project quickly and with less preparation, MIG welding is the way to go.
Understanding the pros and cons of each method will help you make the best choice for your welding projects. Whether you are a professional or a hobbyist, knowing when to use TIG or MIG welding can make a significant difference in the quality and efficiency of your work.
.